1. Introduction
In this tutorial, we will be modeling a quarter of the propeller due to the double symmetry condition. You will also learn how to create a Cell Zone (sub-volume in the fluid zone) - this is to mark the location of the rotating zone. Using the MRF model to introduce a pseudo rotation of the propeller - the propeller will be solved in a rotating reference frame and by this, we introduce artificial motion. It is less accurate than resolving motion directly but is more efficient and allows for steady-state simulation of rotating parts. In advanced post-processing using ParaView we show you how to create an iso-surface of a Q criterion.
2. Download SimFlow
SimFlow is a general purpose CFD Software
To follow this tutorial, you will need SimFlow free version, you may download it via the following link:
Download SimFlow
3. Create Case
Open SimFlow and create a new case named propeller
- Click New
- Provide name propeller
- Click Create to open a new case
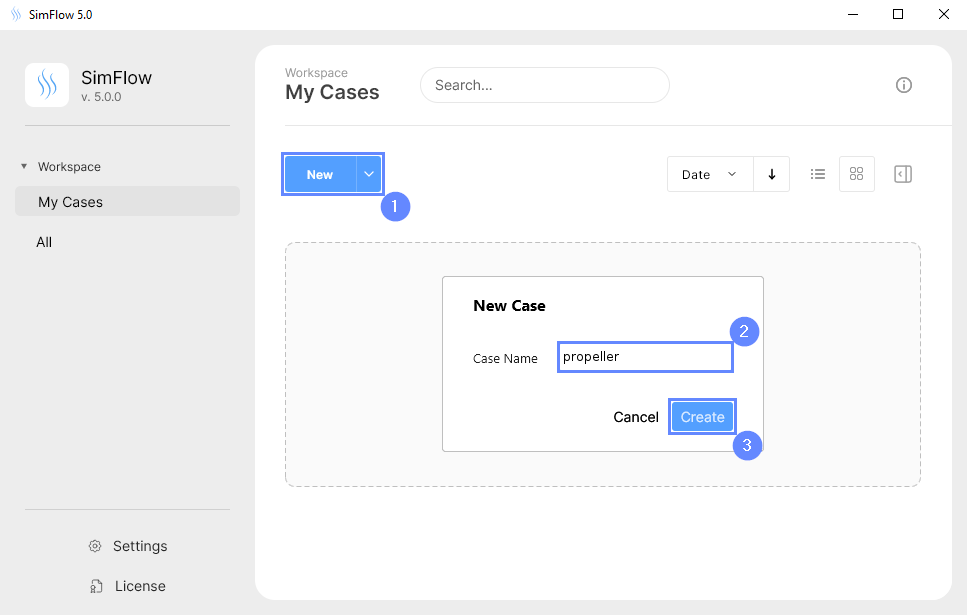
4. Import Geometry - Propeller
After creating case Download GeometryPropeller
- Click Import Geometry
- Select geometry file propeller.stl.gz
- Click Open
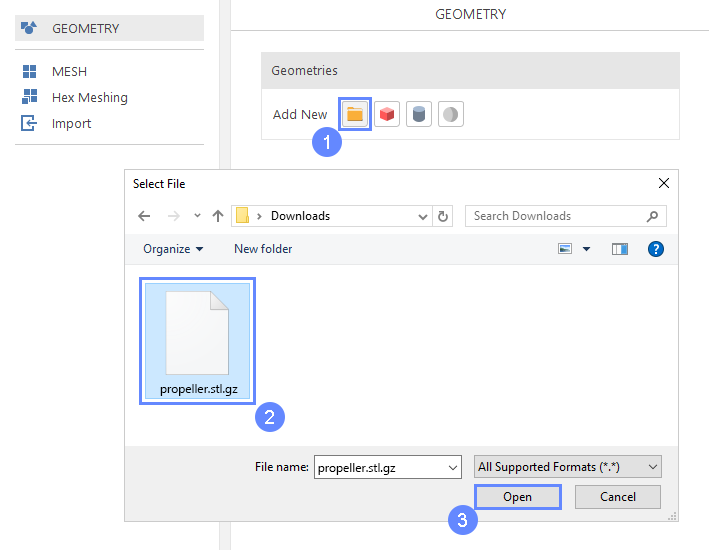
5. Imported Geometry Units
The STL format does not contain the unit information which are defined during the geometry export. If we do not know the exported unit, we can estimate it based on the total size of the model. It is displayed next to Geometry size label. In our case, the default unit meter is correct.
- To confirm default unit meter, press OK
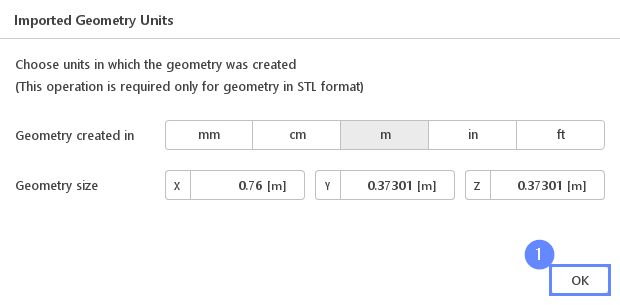
6. Propeller Geometry
After importing geometry, it will appear in the 3D window.
- Click Fit View to zoom the geometry
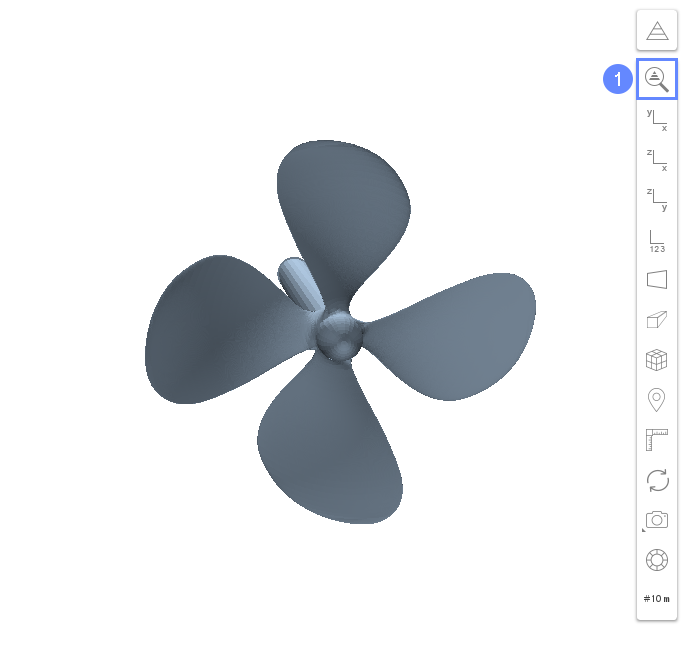
7. Domain Boundary
We need to create a cylindrical boundary for the domain. For this purpose, we will create a cylindrical geometry for later use in the meshing process.
- Click Create Cylinder
- Rename cylinder_1 to external
(double click on the name to rename it, press enter to apply) - Click Properties button if properties panel is not displayed
- Set origin, axis, and length of the cylinder accordingly
Origin \({\sf [m]}\)-1e-0300
Axis \({\sf [-]}\)100
Length \({\sf [m]}\)1.502
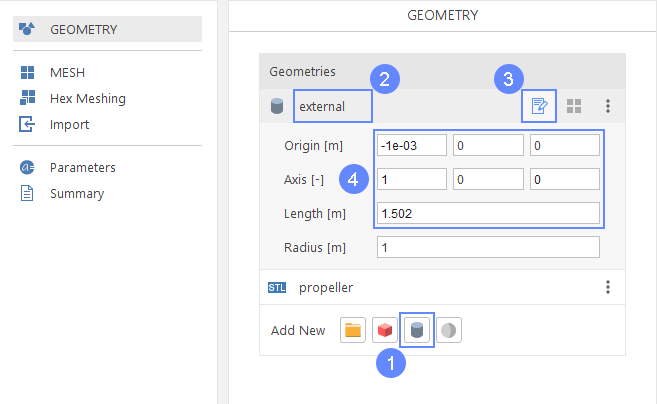
8. Refinement Area (I)
To better resolve the flow near the propeller, we will create an area with a higher mesh resolution. To do this, we will create a new geometry by copying settings from external geometry.
- Click Options of the external geometry
- Select Duplicate option
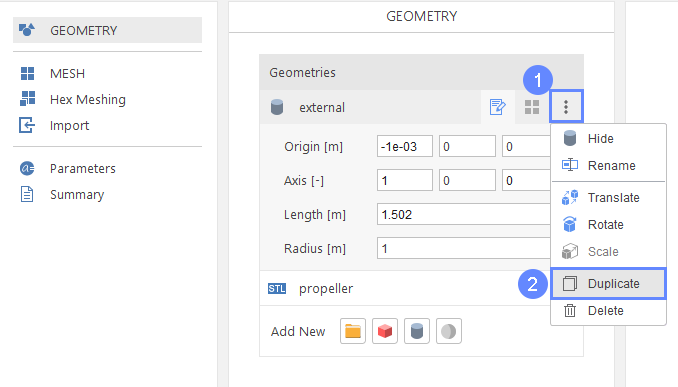
9. Refinement Area (II)
- Click Properties if they are not displayed
- Rename external_1 to refine
- Set radius of the refinement geometry
Radius \({\sf [m]}\)0.3
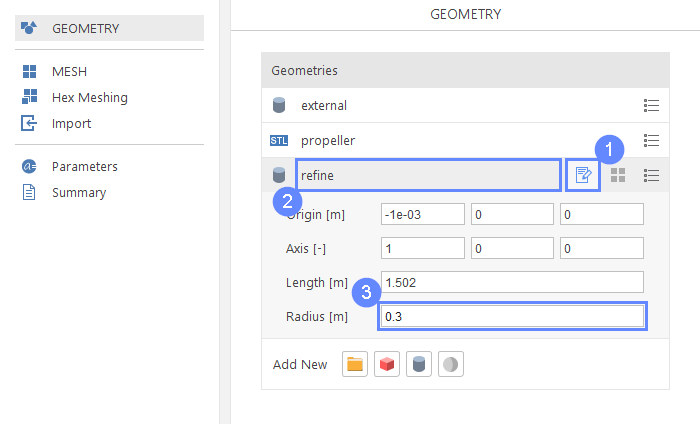
10. Display Geometries
In order to see all geometries, we will decrease the opacity of the external and refine.
- Select external
- Click Display Properties
- Adjust Opacity to 50%
- Adjust opacity to 50% for refine geometry by repeating previous steps
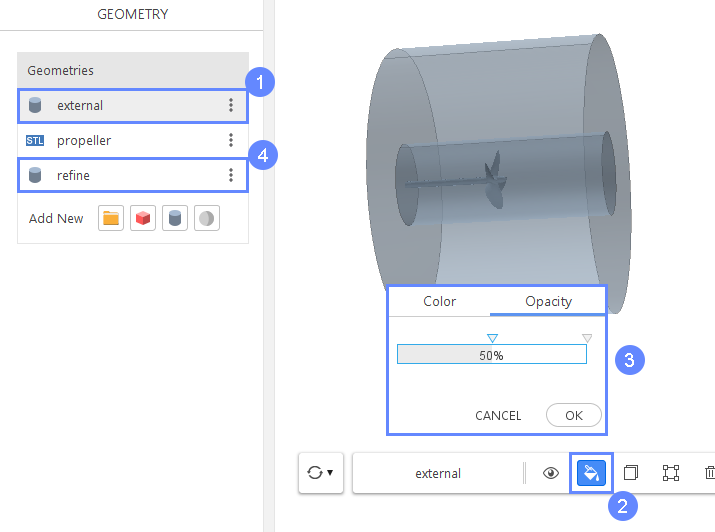
11. Meshing Parameters - External
- Go to Hex Meshing panel
- Enable Mesh Geometry on external geometry
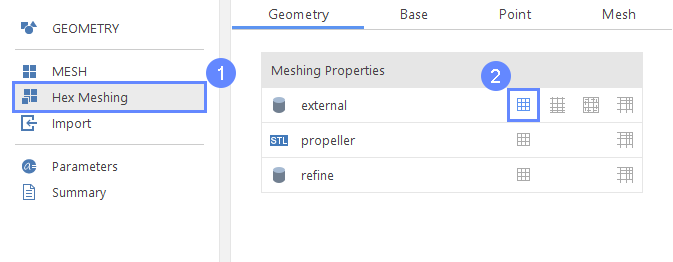
12. Meshing Parameters - Propeller
- Select propeller geometry
- Enable Mesh Geometry
- Enable Create Boundary Layer Mesh
- Set Refinement to Min 3 Max 4
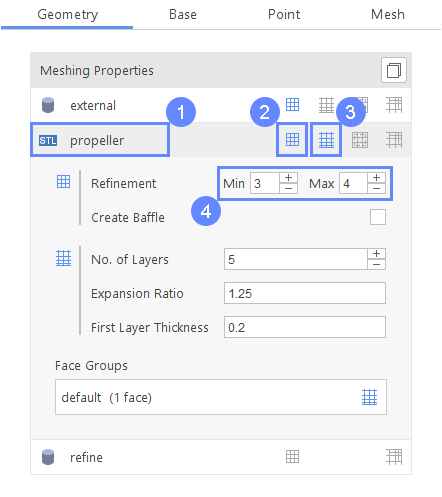
13. Meshing Parameters - Refine
We want to create refinement in the area along the propeller induced flow.
- Select refine geometry
- Enable Mesh Geometry
- Set refinement Level to 2
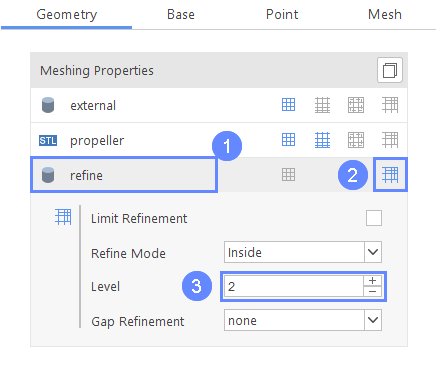
14. Base Mesh
We want to create a mesh of only one blade of the propeller. For this purpose, we will create a base mesh covering only one-fourth of the geometry.
- Go to the Base tab
- Define base mesh minimum and maximum extend
Min \({\sf [m]}\)000
Max \({\sf [m]}\)1.511 - Define Division along each axis
Division302020
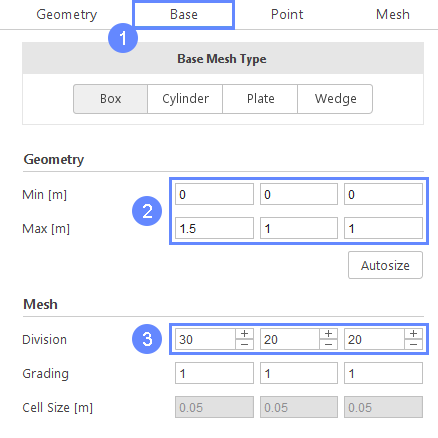
15. Base Mesh Boundaries
- 2 Define boundary names accordingly
X- inlet
X+ outlet
Y- right
Z- left
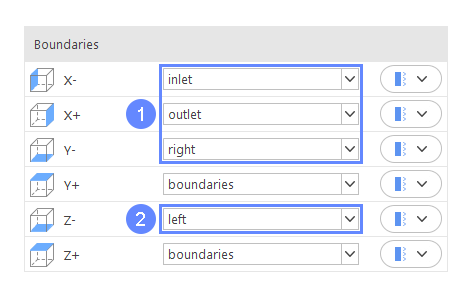
16. Material Point
Now we will define material point outside the propeller geometry.
- Go to Point tab
- Set location of the material point
Material Point0.50.50.5
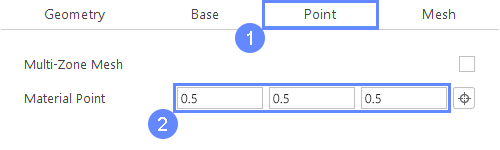
17. Start Meshing Process
- Go to Mesh tab
- Start the meshing process with Mesh button

18. Mesh
After a few minutes of meshing the following mesh should appear.
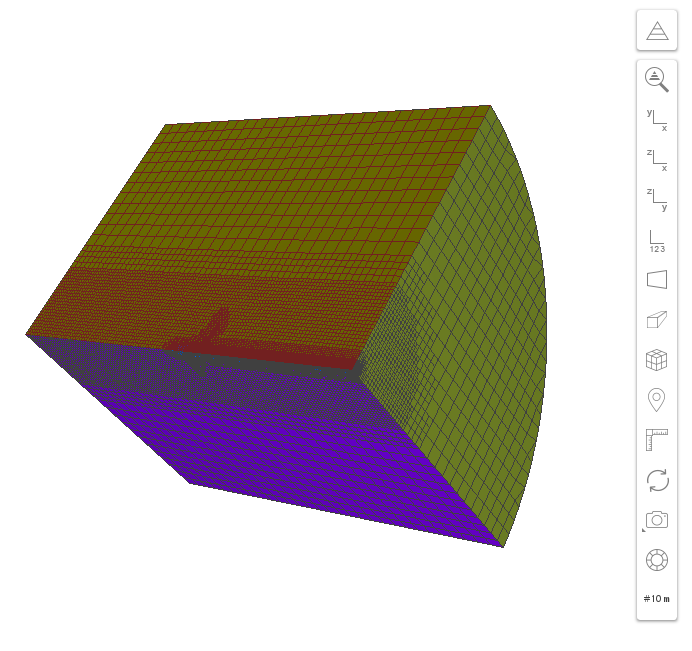
19. Boundary Types
After creating the mesh, we have to set proper boundary types.
- Go to Mesh panel
- Change the boundary type of the external geometry to patch
- Make sure you have appropriate boundary types selected
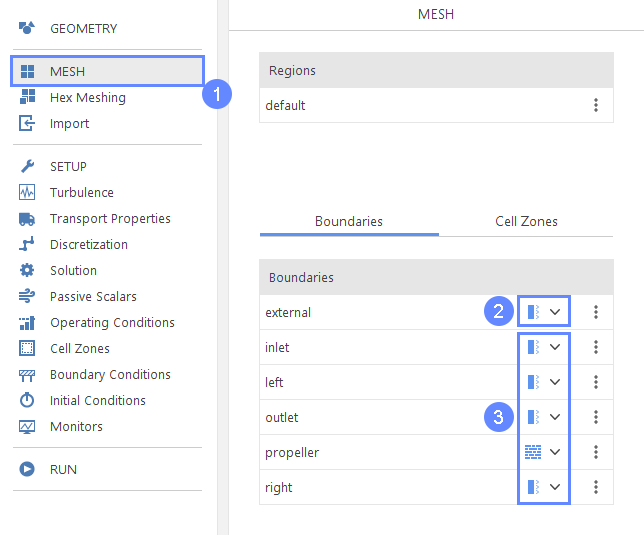
20. Boundary Interface (I)
As we will be simulating only one blade of the propeller we have to create a boundary interface to make the model periodic.
- Hold CTRL key and select left and right boundary
- Click Create Arbitrary Interface between left and right boundary
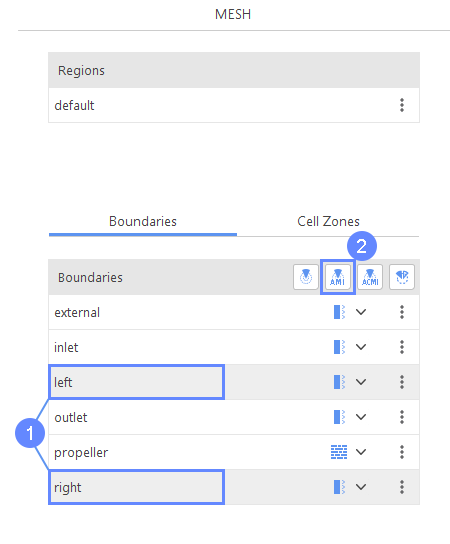
21. Boundary Interface (II)
- Expand the interface properties
- Change Transform type to Rotational
- Define Rotation Axis
Rotation Axis100
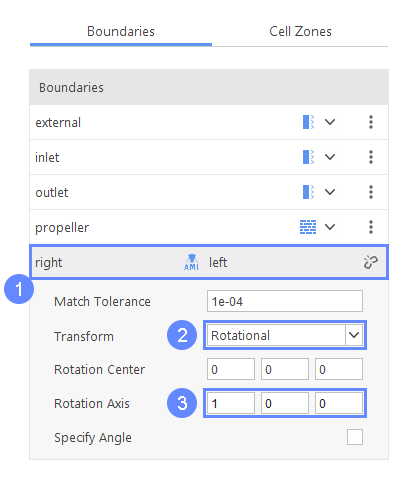
22. Select Solver - SIMPLE
For the simulation of a marine propeller, we will use a steady-state incompressible SIMPLE (simpleFoam) solver.
- Go to Setup panel
- Enable Steady State filter
- Enable Incompressible flow filter
- Pick SIMPLE (simpleFoam) solver
- Click Select button to choose the solver
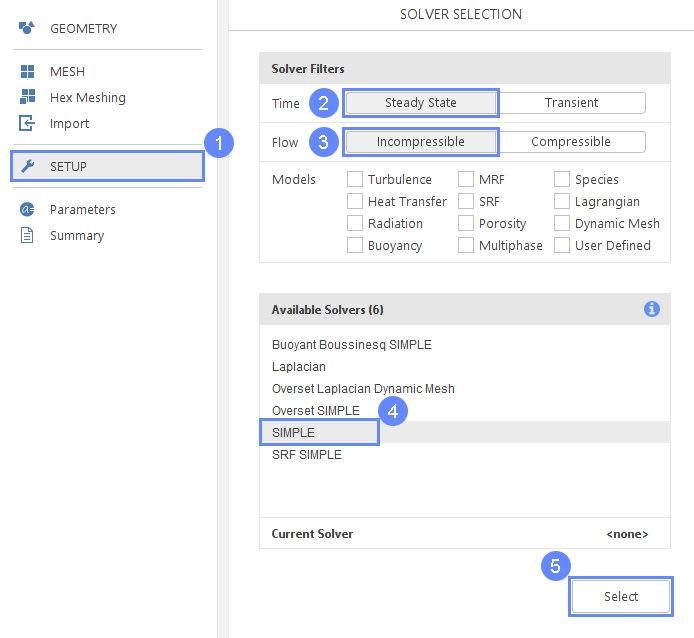
23. Turbulence Model
For the purpose of this tutorial we will simulate the turbulence phenomenon using \(Realizable \; k{-} \varepsilon\) model.
- Go to Turbulence panel
- Select RANS modeling
- Select \(Realizable \; k{-} \varepsilon\) turbulence model

24. Water Properties
- Go to Transport Properties panel
- Define kinematic viscosity of water
\(\nu\) \({\sf [m^2/s]}\)1e-06
Note that you do not have to define density. The equations that describe single phase incompressible flow operates on a kinematic pressure(pressure divided by reference density). Therefore, the density property does not explicitly appear and you have to remember to multiply resulting pressure and forces by the density value to obtain a physical results.
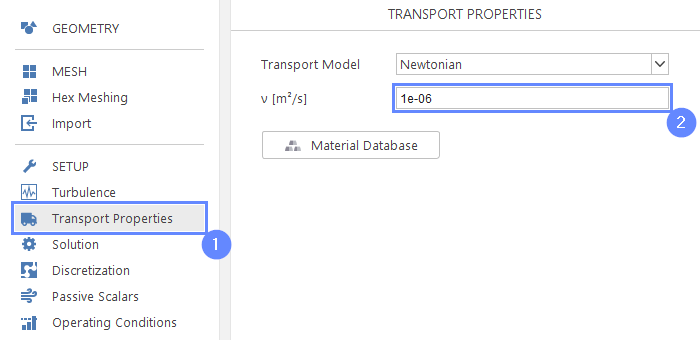
25. Cell Zones for MRF (I)
To be able to model propeller rotation, we will take advantage of a rotating reference frame. This technique will allow modeling the propeller rotation without a need to rotate the mesh. The rotating reference frame can only be applied to a sub-region of the mesh defined by a cell zone object (a list of mesh cells). Therefore, we will first create a cell zone.
- Go to Mesh panel
- Expand list of options form the default region
- Select Add Cell Zones from the menu
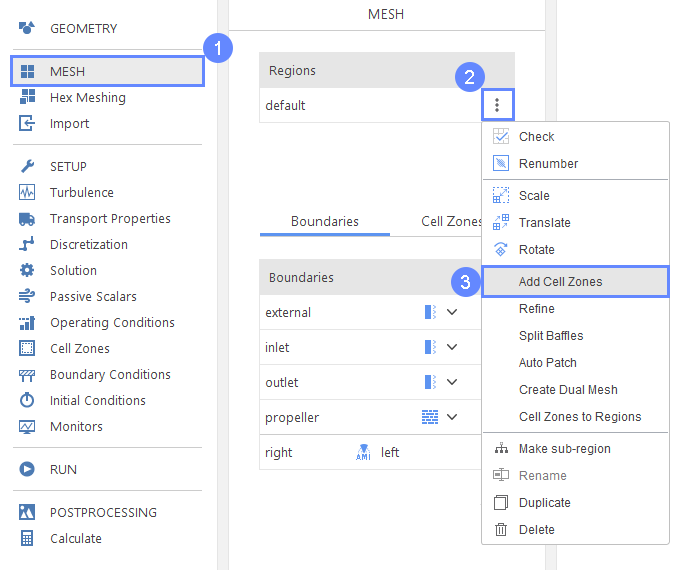
26. Cell Zones for MRF (II)
For the purpose of this tutorial we will use the whole mesh as the rotating zone. To do this we need to create the cell zone inside the external geometry.
- Select external geometry
- Click Create Cell Zones
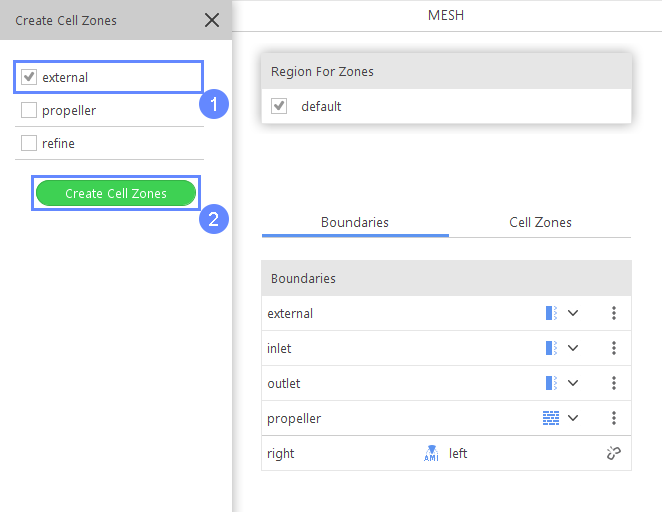
27. Rotating Reference Frame
- Go to Cell Zones panel
- Enable Rotating Reference Frame for external zone
- Define Axis of the propeller
Axis-100 - Select boundaries that will not be defined in the rotating frame of reference
Static Boundaries:
external
inlet
left
outlet
right
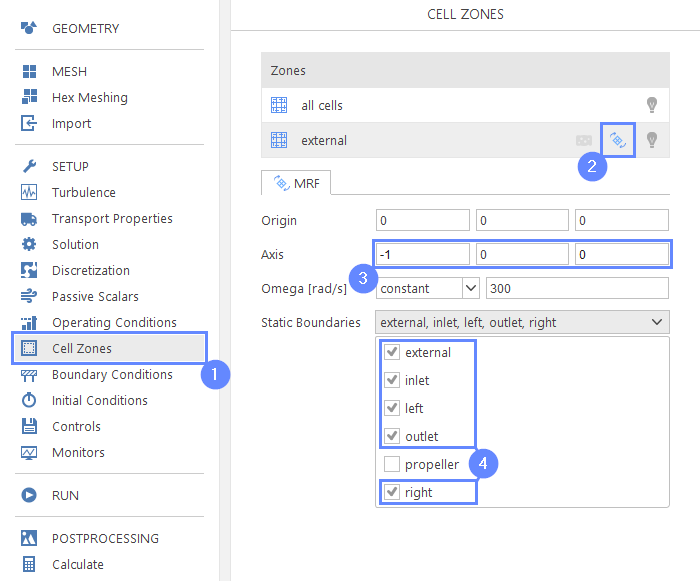
28. Boundary Conditions - External (Turbulence)
- Go to Boundary Conditions panel
- Select external boundary
- Select Turbulence tab
- Set Turbulence Intensity to 1e-02
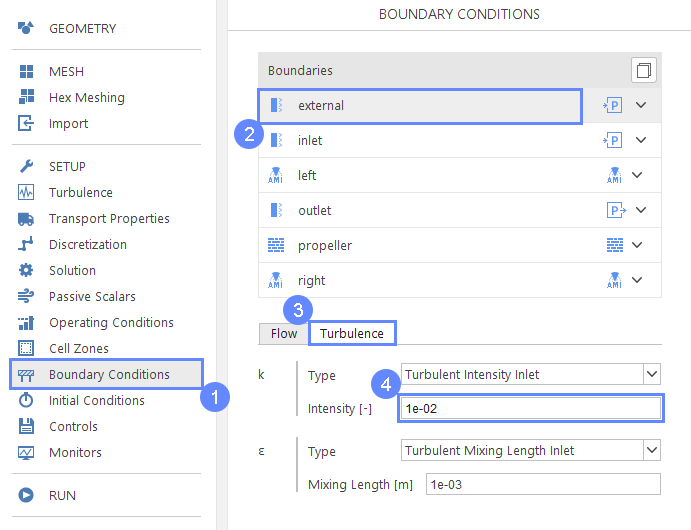
29. Boundary Conditions - Inlet
We will use the same boundary conditions for inlet and external boundaries, to achieve this we can copy settings from the external boundary to inlet.
- Make sure you have selected the external boundary
- Click Copy Boundary Conditions
- Select inlet boundary
- Click Copy
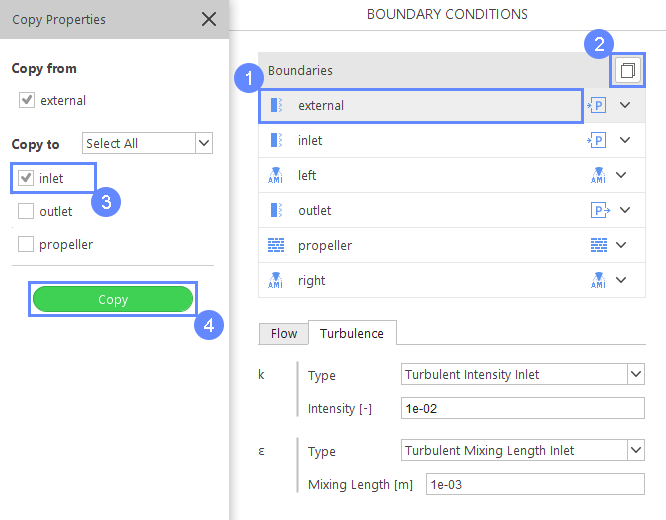
30. Boundary Conditions - Outlet
- Change outlet character to Outflow
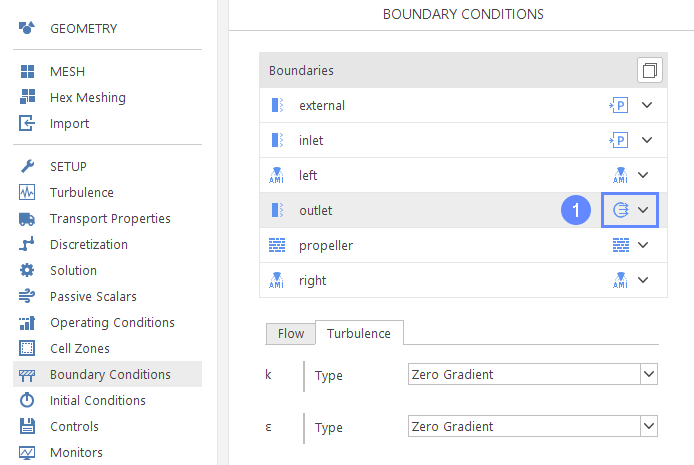
31. Monitor Forces
We want to monitor solution progress by observing force coefficients.
- Go to Monitors panel
- Select Forces tab
- Expand Monitored Boundaries list
- Select propeller boundary
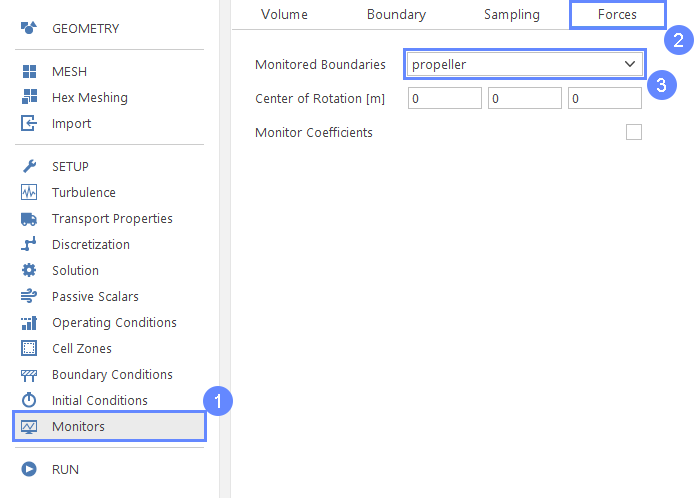
32. Run - Time Control
- Go to Run panel
- Set Number of Iterations to 1000
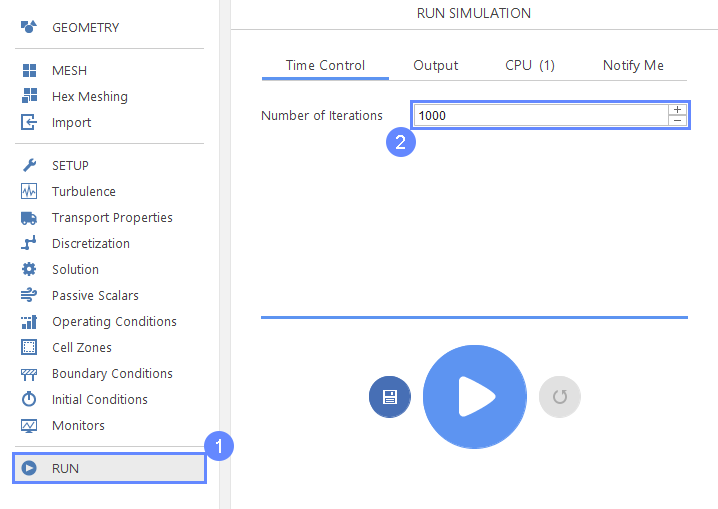
33. Run - CPU
To speed up the calculation process, take advantage of parallel computing and increase the number of CPUs based on your PC’s capability. The free version allows you to use only one processor (serial mode). To get the full version, you can use the contact form to Request 30-day Trial
Estimated computation time for serial mode: 15 minutes
- Switch to CPU tab
- Click Run Simulation button
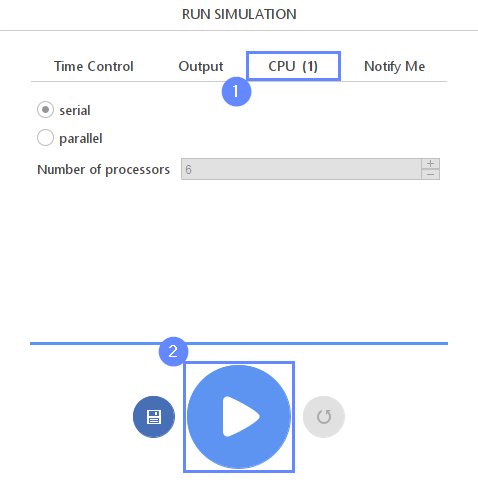
34. Monitor Solution - Force
Check if solution converges by observing stabilization of forces on the propeller boundary.
- Click on Forces tab to display Force Monitor
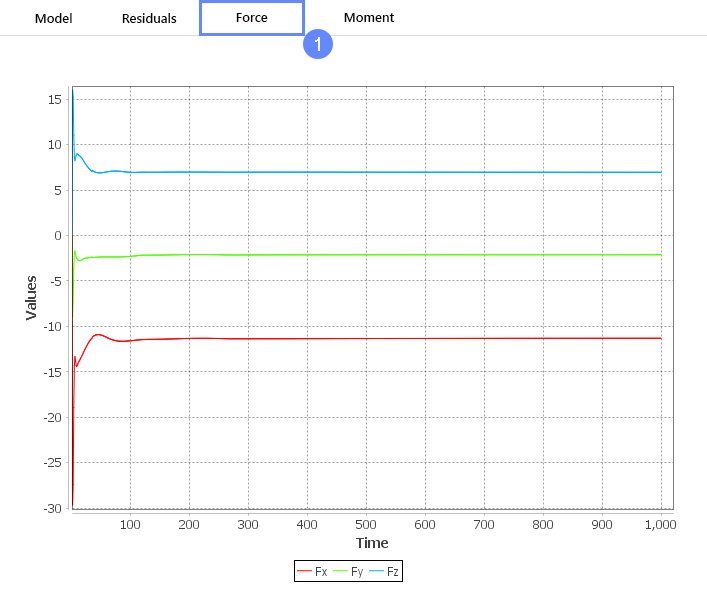
35. Calculate Additional Fields
When a simulation is finished, we want to calculate additional solution field to be used in postprocessing.
- Go to Calculate panel
- Select Q Criterion field
- Calculate the field
Please Note: After clicking the Calculate button, SimFlow will calculate the new flow variable, which will be stored in your project folder and will be accessible in the ParaView.
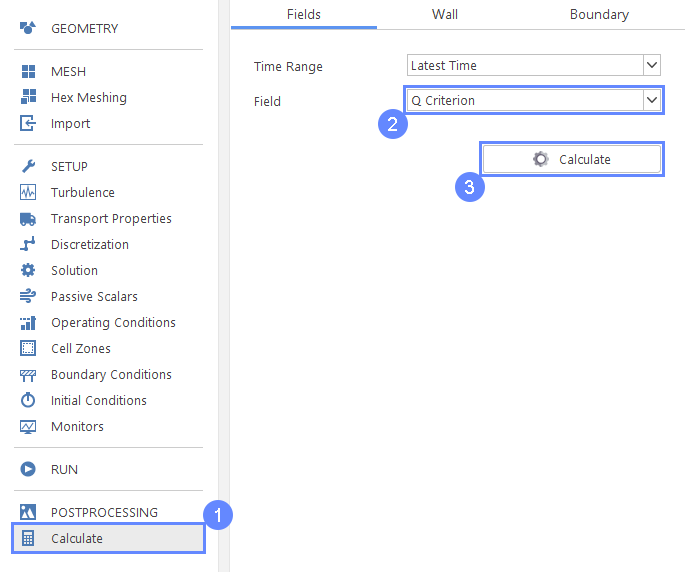
36. Start Postprocessing with ParaView
- Go to Postprocessing panel
- Run ParaView
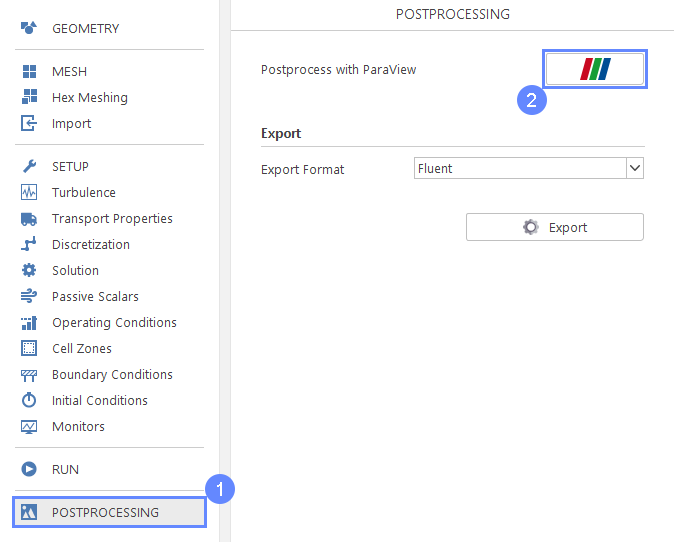
37. ParaView - Load Results
Now we are loading results into the ParaView
- Click Last Frame to select the last result set
- Click Apply to load results into ParaView
- After loading results they will be shown in the 3D graphic window
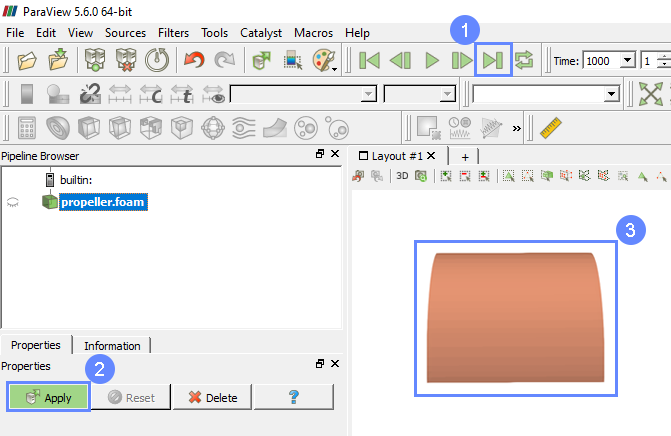
38. ParaView - Display Q Contour (I)
To show the propeller we will create now a contour.
- Make sure you have your case selected
- Click Contour
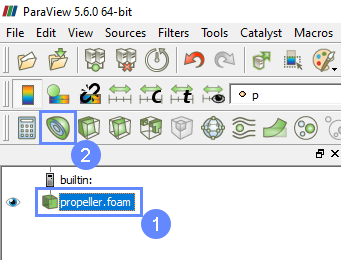
39. ParaView - Display Q Contour (II)
- Set Contour by to Q
- Set contour range to ` 500 ` and click enter
(double click to edit visible value) - Click Apply to create new contour
- After applying changes the contour will be shown in the 3D window
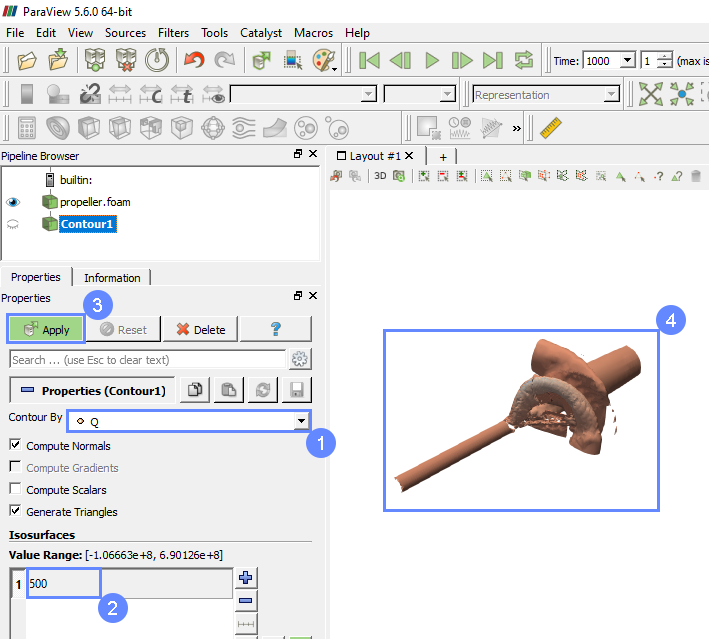
40. ParaView - Show Full Propeller (I)
As you can see there is only a quarter of the propeller visible and we would like to show the full geometry. In order to do that we have to duplicate and transform a partial propeller.
- Make sure you have Contour1 selected
- From the Sources Menu select Search option to open a search window
- Start typing the word transform
- Select Transform option
- Make sure you have Transform1 selected
- Define 90 degree rotation about the X axis and click enter
- Click Apply 2 times to create transformation
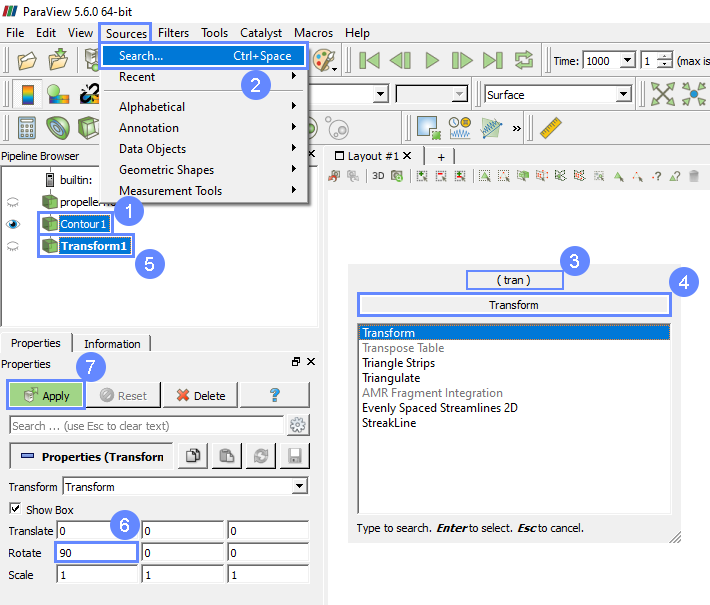
41. ParaView - Show Full Propeller (II)
We have to repeat the previous step to make another transformation - Transorm1 → Transform2
- Make sure you have Transform1 selected
- From the Sources Menu select Search option to open a search window
- Start typing the word transform
- Select Transform option
- Make sure you have Transform2 selected
- Define 90 degree rotation about the X axis and click enter
- Click Apply 2 times to create transformation
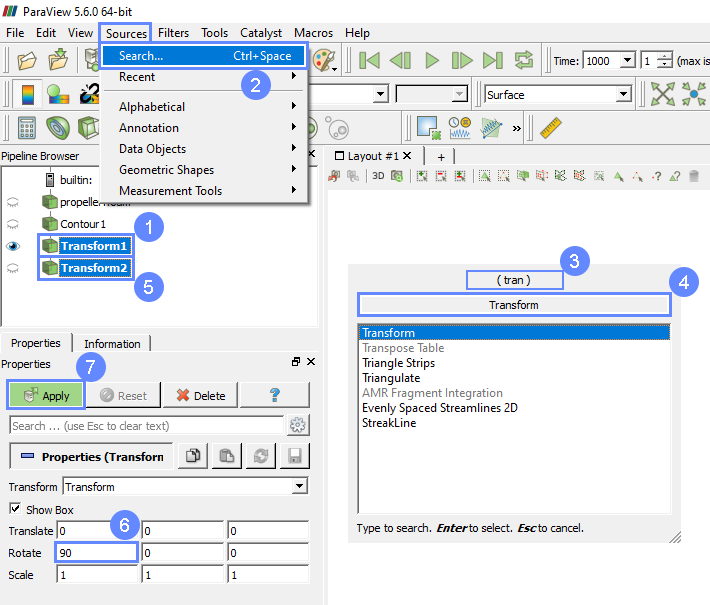
42. ParaView - Show Full Propeller (III)
We have to repeat the previous step to make another transformation - Transorm2 → Transform3
- Make sure you have Transform2 selected
- From the Sources Menu select Search option to open a search window
- Start typing the word transform
- Select Transform option
- Make sure you have Transform3 selected
- Define 90 degree rotation about the X axis and click enter
- Click Apply 2 times to create transformation
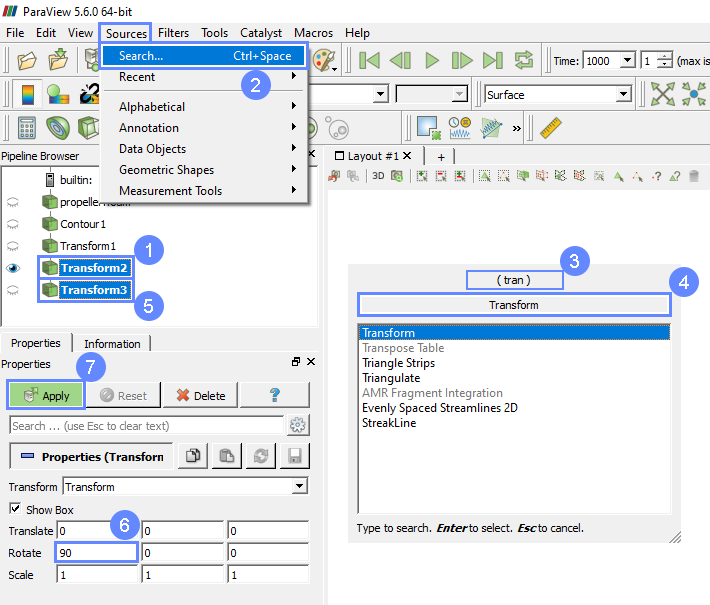
43. Display Full Propeller
To make the full geometry visible, we have to change the visibility of all geometries
- Make sure the contour and all its transformations are visible
- Select Contour1
- Choose pressure p from the coloring list
- Click Toggle Color Legend Visibility and choose Blue to Red Rainbow
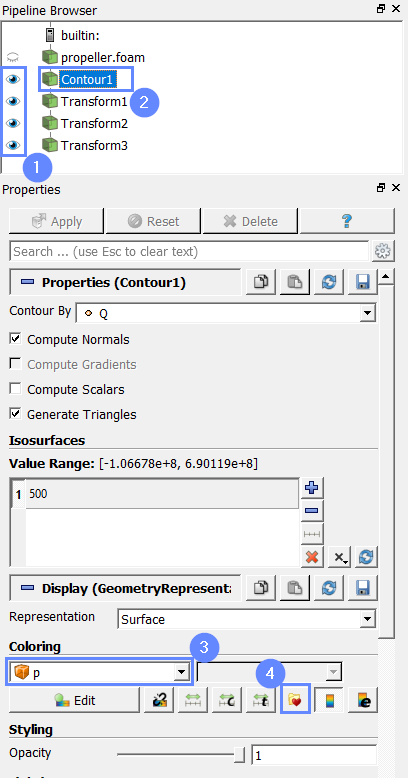
44. Final Results
In the 3D view the contour of full propeller should appear
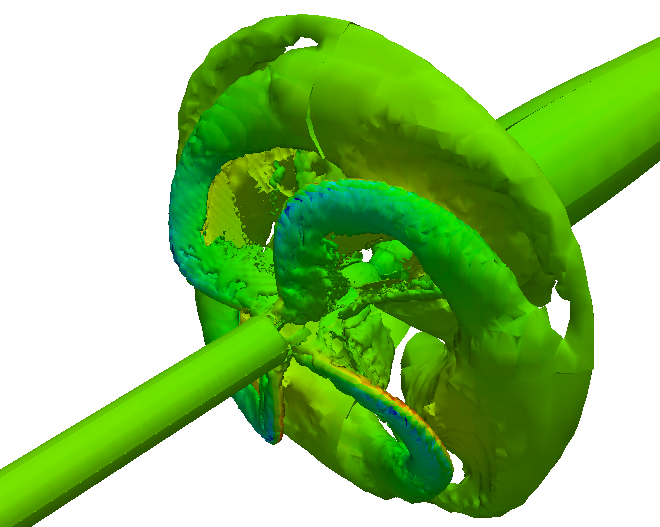
45. Advanced Postprocessing with ParaView
This concludes the tutorial, covering all the aspects we intended to showcase. For a finely tuned presentation of the results, you may take advantage of the more advanced features.
In ParaView, you can display streamlines, contour plots, vector fields, line or time plots, calculating volume or surface integrals and create animations.
To familiarize yourself with the ParaView capabilities, it’s worth checking out our video tutorial, Paraview CFD Tutorial - Advanced Postprocessing in ParaView, in which we demonstrate some of the most commonly used post-processing techniques.